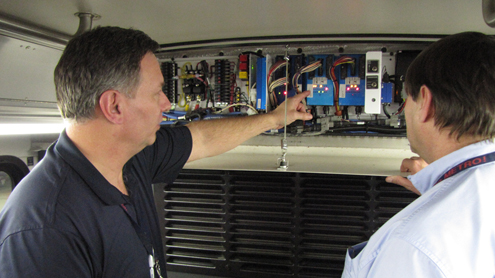
Metro St. Louis employs predictive monitoring to foresee component failures
By David Hubbard
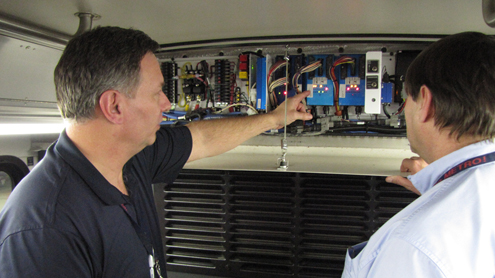
Predictive monitoring lies somewhere between a sixth sense and standard preventive maintenance, and essentially serves technicians as a crystal ball to foresee equipment failures. The technology personalizes each bus in the fleet, eliminating any generalization as to why and when to send a particular vehicle in for maintenance.
Metro St. Louis, St. Louis, MO, is a diverse agency that operates the entire public transit network comprised of MetroBus, MetroLink light rail and Call-A-Ride paratransit. It transports sightseers on trams to the top of the landmark Gateway Arch and on Mississippi riverboats, and manages the St. Louis Downtown Airport.
Already recognized for its outstanding maintenance operation, the agency has adapted this relatively new data analysis system to its bus fleet. It first engaged in predictive monitoring in 2005 when it signed on with Accenture Technologies, Chicago, in a pilot program to equip 20 buses with special engine and transmission sensors to monitor performance.
Additional real-time sensors attached to the vehicle-monitoring unit enabled the predictive monitoring system to analyze more data than what standard engine sensors typically deliver. The objective was to cut costs and improve system-wide performance by reducing vehicle failures and streamlining maintenance schedules.
The sensors monitor road speed, engine speed, engine load, cooling temperatures, oil pressure, fuel consumption, as well as ambient temperatures outside the bus. The information feeds to a central computer for analysis and follows with an Internet presentation to service technicians.
“Every bus in the fleet is a little different,” says Ray Friem, Metro St. Louis chief operations officer, transit division. “Each vehicle has its own quirks and operates under separate conditions. Before we try to find out what is wrong, we want to understand the performance of each bus when it is just humming along.”
Metro St. Louis passed on the Accenture Technologies pilot, choosing instead to develop its own analytical model.
“We felt we were a little ahead of the curve in this area,” says Friem. “We found the pilot program we tested very capable, and would certainly work well for most agencies. We just knew what we were looking for in such a system and believed we had the capability to custom build to our own specifications.”

Friem sees traditional maintenance involving routine schedules coming either too late or too soon — using the data to understand only what happened when components fail and vehicles breakdown.
Predictive monitoring compares real-time data to normal parameters established in the model. Any deviation from the norm translates as a triggering event that suggests the type of failure that is in store, and predicts when it is likely to occur.
For example, advance warning in one vehicle pointed to an overheating hydraulic retarder. Though the problem was not severe or dangerous at that moment, early detection prevented a minor problem from developing into a costly repair.

“Predictive monitoring does not reveal anything experienced mechanics have not seen before,” says Friem. “But these diagnostics provide empirical and timely evidence, which enables us to manage our maintenance schedules more precisely without wasting time and money.”
After categorizing all the defect card information — how many and what kind — and determining which age category they fell into, the team compared the data to the repair tickets to when and where the agency invested to fix each vehicle.
Laying out the parameters in his Preventative Maintenance Initiative, he and his team created the predictive monitoring model he calls the Pseudo Bus.
“Our guys in the shop just call all of this The Plan,” he says. “This marked the first time we had ever asked what our business plan was in terms of maintenance.”
The Plan basically analyzes the fleet with respect to the age of each bus. It categorizes the buses accordingly: first three years; four to six years; seven to nine years; 10 to 12 years, and 13 to 15 years, as Metro St. Louis tends to operate older vehicles. Friem determined on closer examination, 80 percent of the maintenance costs, which he deems an investment, went to equipment due for retirement within two years.

The Plan broke into a mileage-based system and developed repair activities in advance of component failure. For example, it was determined that a specific type of transmission would fail between 200,000 and 300,000 miles, and an overhaul effort was established at the 200,000 mile mark. Friem says predictive monitoring is clearly taking the fleet maintenance effort to the next level.
“Where we were overhauling a transmission religiously at 200,000 miles, we found it to be failing at 260,000,” he says. “The new system showed us statistically it probably had 40,000 of good life remaining. This told us we might have been making our maintenance investments too soon.”
Under the new predictive program, the technicians poured over every component on nearly 320 buses from 2000 forward to determine the time a part has left before failure from the moment the primary triggering event occurs.
Friem reports that the predictive maintenance program has already directly saved Metro St. Louis nearly $5 million a year and at the same time, saved another $5 million in personnel-related costs.
“Applying this new philosophy has truly shifted how this agency approaches maintenance,” says Friem. “Now a failure of any sort is something we take very personally.” BR