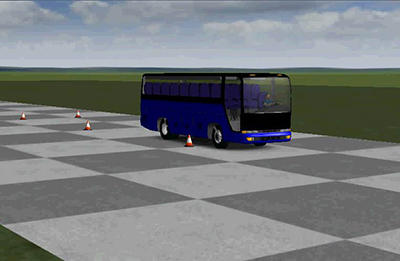
By Gerry Remus
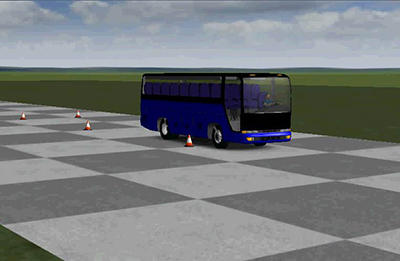
As urban population trends continue to rise, so has the need for an infrastructure to handle these increasing demands. A tremendous opportunity exists for buses to satisfy the need to transport the growing population in a safe, reliable and comfortable manner. Bus manufacturers are challenged with providing solutions that can maximize the number of passengers, maintain the highest level of durability and to ensure passenger safety and comfort. The suspension system and axles are at the root of the bus experience and influence the vehicle in three primary ways: safe handling for the driver, ride comfort for the passengers and reduced vibration that saves wear and tear on the bus body and other components. Bus operators tend to think of ride comfort first when they make the move to an air suspension system. However, suspensions protect more than just the passenger; contributing to safe handling as well as ensuring long life for the vehicle, a substantial investment.
While buses around the world may have a similar look and feel, the passenger and equipment loads, environmental factors, road conditions and braking cycles can vary greatly between countries, states and even cities. For example, the potential to overload a transit bus operating in the U.S. is unlikely. However, in more populated countries, such as India and China, overloading can account for up to 40 percent of the rated capacity of the suspension. For these reasons, one suspension will not fit for all markets and consideration must be given to these regional differences to ensure optimal performance.
Understanding ride comfort
A principle function of the suspension system is to absorb as much of the vibration and harshness as possible. Ride quality hinges on the degree of isolation the suspension provides the vehicle from vibration and road inputs. It is a measure of how road shock affects the vehicle, driver and passenger as the vehicle encounters bumps, potholes or other road irregularities. Air bags and shock absorbers work together to offer a smooth ride with one passenger on board or with 50. The challenge is to build in ride comfort while maintaining roll stability and vehicle handling. Not all suspensions are created equal, so choosing the right suspension to meet the needs for a given application is critical.
Hendrickson, for example, places high value on relationships with bus manufacturers to understand their expectations, needs and wants. The bus OEM typically defines the desired ride quality for their product. In some instances, vehicle handling may be more critical than ride comfort or roll stability may be the priority for the OEM.
Once the goals for ride quality are set, building in ride comfort begins by collecting data that defines the application. Hendrickson takes a total vehicle approach, understanding how products are influenced by other chassis components and what factors can change performance. Before design work begins, it is essential to understand everything possible about the environment that the bus will be operating in. Hendrickson goes to great lengths to collect real-world data to determine the specifications necessary to maximize performance and durability. Extensive data collection from the field along with customer interviews and site visits enable Hendrickson to get a true understanding of what a product must endure while in operation.
Ensuring durability and performance
Understanding real-world scenarios is essential, but this alone is not enough to bring a solution to the market. Hendrickson invests in the most advanced engineering software to model specific components, identify stress points and simulate suspension performance in different application environments and load conditions. As the design matures, sophisticated in-house research and development facilities are utilized, featuring numerous test rigs designed to simulate real-world scenarios, to ensure that reliability, performance and quality objectives are met before finalizing the design. Once a suitable design has been created, track testing commences and final design refinement occurs as the product endures tests that emulate real-world conditions and are correlated to industry or OEM test tracks. In proving-ground testing, Hendrickson utilizes test tracks that replicate the actual Altoona test track so that a firm understanding of durability and performance are well known.
Hendrickson has a rich history of providing the right product for the right application, which requires a series of critical steps to ensure many years of successful operation in the field. As the bus market needs continue to evolve, Hendrickson stands ready to support our customers, developing solutions that exceed expectations for performance and durability.
Gerry Remus serves as business unit director – Global Bus for Hendrickson Commercial Vehicle Systems, Woodridge, IL. Visit Hendrickson online at www.hendrickson-bus.com