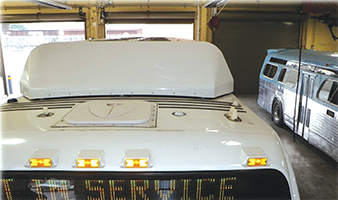
By Alice Wilson
Bus purchases make up the majority of all capital costs for the average transit agency. According to the 2014 American Public Transportation Association (APTA) Factbook, there are 2.75 billion rolling stock vehicles currently in service nationwide. Bus prices can range from $400,000 to $700,000 or more based on size, manufacturer, chassis configuration and number of buses ordered. Typically paid as up-front costs with a useful life expectancy of 12 years, investing in rolling stock is big business.
Buses today roll off the assembly line packed full of technology. There are on-board diagnostic tools that monitor safety features, fuel systems, intelligent transportation systems, mechanical components and information systems to measure vehicle health and operational performance. These on-board tools are just that… on board. The ability to share, analyze trends and remotely report the status of these systems hasn’t advanced as much as the in-vehicle technology itself. Currently the most consistent in-vehicle diagnostic information received by agencies comes in the form of the reactive Man Machine Interface (MMI) which requires the driver to monitor audio and visual notification systems in-person and communicate their observations to dispatchers. There are some in-vehicle diagnostic systems that utilize GPS, Wi-Fi, and cellular communications to transmit data. Being proprietary in nature, they do not share data airspace and they require a separate antenna for each system being monitored.
- Something as simple as multiple antennae on the rooftop of a bus can open agencies up to areas where mechanical faults can result.
Challenges of current in-vehicle diagnostics Agencies trust the health of their very expensive sub-components to reactive data prone to human error. Unable to be properly analyzed through trending information, small inexpensive issues can quickly grow into significant costly problems that could compromise reliability and quality of service. Even something as simple as multiple antennae on the rooftop of a bus opens the agency up to areas where a mechanical fault can result. More antennae means more holes, which means more of a chance for damaging leaks to permeate the outer shell of the bus. It also increases the likelihood of damage to the antenna itself, resulting in expensive repairs, replacement or interruption of system monitoring. In-vehicle diagnostic systems that require maintenance personnel to use disparate software to even identify a problem are not only cumbersome and inefficient, they also lend themselves to being under-utilized, affecting overall fleet performance and reliability.
What the industry needs today
Right now the industry has bus components equipped with electronic sensors that identify failed, failing or maladjusted conditions as it relates to powertrain alarms, propulsion, braking, HVAC, fluid levels, electrical, ITS and on-board equipment systems. Agencies are equipped to react to the breakdown of components. A part breaks. Maintenance staff uses the tools in their toolbox to fix it, and the bus is placed back into revenue service. But how long will the repair last? How reliable is that fix? What the industry needs today is a transit-smart toolbox that equips maintenance and operational staff with Maintenance Intelligence (MI). Focused on Key Performance Indicators (KPIs), Maintenance Intelligence gives your agency all the diagnostic data across every device at a glance and presents it to staff seamlessly in one centralized location. Fully compatible with any agency’s CAD/AVL system, MI puts real-time maintenance data in the hands of those who drive the business every day. Maintenance Intelligence allows staff to evaluate condition-based maintenance as part of overall vehicle health monitoring and remote vehicle diagnostics.
With MI, failure prediction capabilities become a reality by utilizing configurable tolerance conditions that automatically warn staff when a sub-component is failing or maladjusted. There’s no longer a need to solely rely on communications from a driver about failed parts, or wait for the bus to return to the garage to be inspected by a technician. This means maintenance staff can be proactive, working to prevent breakdowns before a part fails and thus minimizing repair costs behind the scenes with little to no impact on quality of service. Maintenance Intelligence also give agencies the capability to analyze mechanical trends not only for individual parts, but also across manufacturers, makes, models, even production years to know what the most reliable pieces of equipment are. The use of one centralized on-board computer that connects to all of the sub-components eliminates the need for antenna farms, still allowing an agency to gather data while the bus is on the road.
The benefits of maintenance intelligence
Using MI, agencies can reduce in-service breakdown instances and improve overall fleet capability to enhance rider experience while providing an unsurpassed quality of service. The reduction of false alarms and the ability to analyze and calculate the cost of breakdown repair versus preventative maintenance helps optimize operations by saving time and money. Centralized data allows agencies to gain fleet-wide perspective to make transit-smart business decisions. This same data can be shared with peer agencies to help create a cohesively reliable fleet that connects a regional community. Comprehensive information that can be shared with manufacturers will help them improve their product offerings, resulting in safer and more reliable buses to your doorstep. With Maintenance Intelligence, everybody wins.
Alice Wilson serves as product manager for Avail Technologies, State College, PA, an ITS technology solutions provider for transit operators throughout the United States. Visit www.availtec.com for more information.