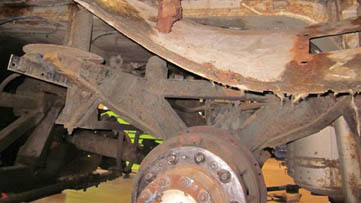
Budget Truck and Auto repairs the corroded tubing in three stages
By Joel Salter

Winters in Wisconsin are particularly brutal on vehicles maneuvering in cold wet weather on salted roadways. As a result, Budget Truck and Auto, Janesville, WI, has become expert at one particular climate-related refurbishment procedure on late model 1990s MCI D coaches and the longer MCI DL3s: the replacement of eroded air bag support structures and repair of any ensuing damage to the flooring.
Six airbags, each approximately one foot in diameter, support the rear axles — four on the drive, two on the tag axles with two structural tubes for each airbag fitted in the framework to hold them in place.
Typically, especially in the winter months, the surrounding insulation gets damp and holds in moisture. Over time the tubing supports simply rust out and corrode to the point of crumbling. With the tubing gone there is nothing more than a layer of sheet metal separating the airbags from the flooring on the inside of the bus.
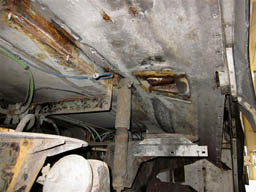
With nothing to support the airbags, the force from the suspension pushes them upward into the plywood flooring beneath the seats over the wheels.
As the damage can become more severe the longer it goes undetected, Budget Truck and Auto has designated three stages for what it calls Airbag PM based on the extent of the corrosion. The first step is always a pre-inspection to diagnose the damage and determine the method of repair. Budget Truck and Auto has adapted a replacement kit from MCI to better suit the situations common to this region.
Level One
If operators detect this damage in time and the airbags have not pushed up into the floor inside the coach, the least invasive process is to make all the repairs from the outside. Technicians simply replace the airbags. They put the coach on lifts, remove the rear wheels, remove the old airbags and cut out the existing supports.
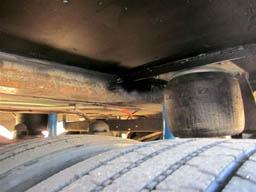
They build a new structure that fits on the bottom of the splash shield that supports the airbags, as well as a new plate out of quarter-inch steel for the airbag to rest on and support the vehicle.
Level Two
If the tubing is gone and the flooring is not to the point the airbags have pushed up through the floor, but are starting to push against the sheet metal, replacement of the floor structures above the airbag is still possible from underneath.
Technicians not only replace the airbag support, but if necessary the tubing above the airbag supports extending up about 3 inches that supports the plywood floor.
Level Three
Once the airbags have actually pushed up the floor it is necessary to work from
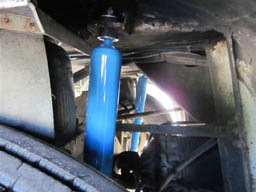
inside the coach to remove the seats and replace the warped and sometimes broken plywood sections. This also requires additional undercoating and sealing to waterproof the new materials.
This more involved procedure is rare and easily prevented through routine vehicle inspections and preventive maintenance. Over the last few years, Budget Truck and Auto has only had five instances in which the crew had to go in and pull seats.
Technicians will usually replace the airbags as part of this process regardless of the level of damage. If they were never replaced prior to this, they would mostly likely be in the same bad shape as the other components. Usually the floor supports are so rusted and corroded that the nuts connecting the airbags are impossible to loosen. Once the technicians have removed the airbags, replacing them as part of this repair also saves on overall labor costs. BR